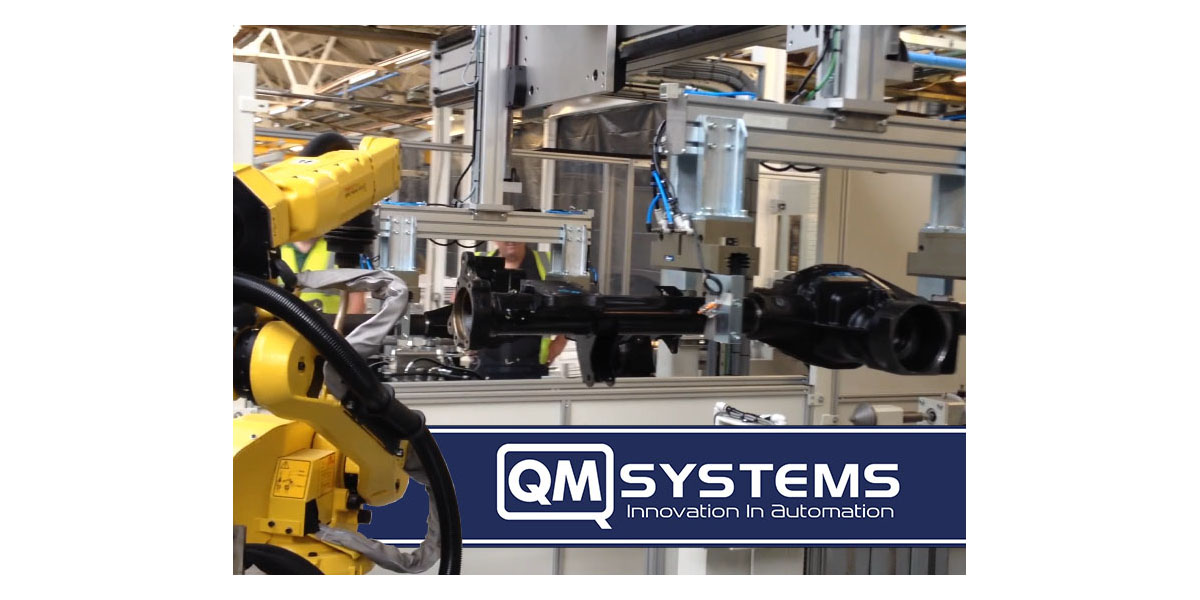
Directech QM-Systems had a requirement from a Nationally recognised automotive client to automate the puddle weld process for three variants of vehicle axle. Our solution consisted of a two station HepcoMotion rail driven system. The system uses servo drives to accurately position the component into the relevant station.
An operator manually loads the axle components into the hydraulic press using a manipulator arm. Once in place, clamps press down on the central differential, and the hydraulic press assembles the parts together. An overhead gantry containing 2 pneumatic heavy duty grippers moves into position over the axle assembly. It then lowers and picks the axle out from the nest. The gantry moves the assembly into the weld cell, and loads it into the fixture.
The loading fixture is located between two positioner units, which are capable of rotating 180° to allow all of the puddle weld positions on the axle to be easily accessible. An auto change location fixture is also present in order to accommodate all three variants. This is operated using a Siemens PLC/HMI. Once the assembly is placed, the gantry retracts and two FANUC Europe Arc Mate 100IC-12 welding robots, each attached with a Fronius International TPS 500i PULSE weld system move into position. They weld the axle where required.
When the welding is completed. The rear gantry lift assembly lowers over the finished axle and removes it from the cell. The assembly is transitioned and placed on an awaiting pallet, located on a conveyor system to take it to the final assembly station also designed by Directech QM-Systems. At the same time, the front lift assembly picks up the next axle assembly from the hydraulic press station and loads it into the welding cell.